Mastering Stock Allowances: A Comprehensive Guide to Optimizing Machining Operations
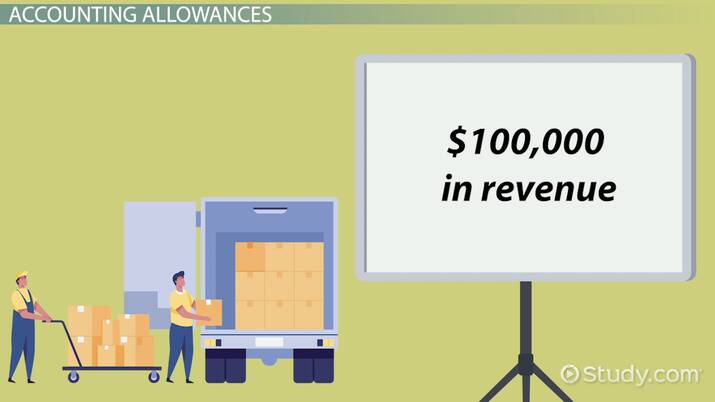
In the realm of computer-aided manufacturing (CAM), defining stock allowances is a critical step in achieving precise, efficient, and cost-effective machining operations. Stock allowances, also known as machining allowances or material removal allowances, refer to the additional material intentionally left on a workpiece to accommodate subsequent machining operations, achieve final part dimensions, and ensure dimensional accuracy and surface finish quality. In this comprehensive guide, we’ll explore the importance, methods, considerations, challenges, and best practices associated with defining stock allowances in machining processes.
Understanding Stock Allowances
Before delving into the details of defining stock allowances, it’s essential to understand their significance and objectives. Stock allowances serve several key purposes:
- Compensating for Material Variability: Stock allowances account for material variations, such as surface roughness, material hardness, and dimensional inaccuracies, inherent in raw material stock, ensuring that final part dimensions meet design specifications.
- Facilitating Subsequent Machining Operations: Stock allowances provide sufficient material for subsequent machining operations, such as finishing, milling, drilling, and threading, enabling the removal of excess material to achieve final part dimensions and tolerances.
- Minimizing Scrap and Rework: By providing a margin of material for machining, stock allowances reduce the risk of undersized or defective parts, minimizing scrap rates, rework, and material waste.
- Optimizing Tool Life and Surface Finish: Stock allowances allow for conservative cutting parameters and toolpath strategies, reducing cutting forces, tool wear, and surface roughness, resulting in improved tool life and surface finish quality.
Importance and Benefits
Defining appropriate stock allowances is essential for achieving optimal machining performance and part quality:
- Dimensional Accuracy: Properly defined stock allowances ensure that final part dimensions and tolerances are met, reducing the risk of dimensional inaccuracies and deviations from design specifications.
- Surface Finish Quality: Stock allowances enable the removal of surface defects, imperfections, and tool marks left by previous machining operations, resulting in improved surface finish quality and aesthetics.
- Tool Life Optimization: By providing adequate material for machining, stock allowances minimize tool deflection, vibration, and wear, extending tool life and reducing tooling expenses.
- Process Efficiency: Optimized stock allowances streamline machining operations, reduce machining time, and improve productivity by minimizing material removal requirements and maximizing machining efficiency.
- Cost Reduction: Reduced scrap rates, rework, and material waste resulting from well-defined stock allowances lead to cost savings and improved profitability in manufacturing operations.
Methods for Defining Stock Allowances
Defining stock allowances involves several methods and considerations, depending on the specific requirements of the machining process and the characteristics of the workpiece:
- Engineering Drawings and Specifications: Stock allowances are typically specified in engineering drawings, CAD models, and machining specifications provided by design engineers or manufacturing engineers, indicating the required material removal allowances for each machining feature.
- Material Properties and Machinability: Considerations such as material hardness, machinability, and surface finish requirements influence the selection of appropriate stock allowances, with harder materials typically requiring larger allowances to accommodate tool wear and material removal rates.
- Machining Process and Cutting Parameters: The selection of cutting parameters such as cutting speed, feed rate, depth of cut, and toolpath strategies affects the amount of material removed per pass and, consequently, the required stock allowances.
- Experience and Best Practices: Leveraging experience, best practices, and industry standards for similar machining operations helps guide the selection of stock allowances based on past successes and lessons learned.
- Simulation and Prototyping: Performing simulation studies or prototyping trials allows manufacturers to evaluate different stock allowance scenarios, assess their impact on machining performance and part quality, and optimize stock allowance definitions accordingly.
Challenges and Considerations
Defining stock allowances poses several challenges and considerations that must be addressed to ensure optimal machining results:
- Material Variability: Variations in material properties, such as hardness, grain structure, and residual stresses, can affect material removal rates and surface finish quality, necessitating adjustments to stock allowances.
- Tool Wear and Deflection: Tool wear, deflection, and cutting forces vary depending on cutting parameters, tool geometry, and material properties, requiring careful consideration when defining stock allowances to ensure adequate material removal and tool life.
- Surface Finish Requirements: Tight surface finish requirements may necessitate smaller stock allowances to minimize material removal and achieve the desired surface finish quality without excessive machining.
- Complex Geometries: Machining complex geometries with intricate features and varying material thicknesses requires careful consideration of stock allowances to ensure uniform material removal and dimensional accuracy across the workpiece.
- Cost and Time Constraints: Balancing the need for precise machining with cost and time constraints is essential when defining stock allowances, as overly conservative allowances may lead to excessive material removal, longer machining times, and increased production costs.
Best Practices for Defining Stock Allowances
To maximize the effectiveness and reliability of stock allowances, manufacturers should adhere to best practices:
- Collaborate Across Departments: Foster collaboration between design engineers, manufacturing engineers, CAM programmers, and machinists to ensure that stock allowances are accurately defined and integrated into machining processes.
- Document and Communicate: Document stock allowance requirements in engineering drawings, CAD models, machining specifications, and work instructions, and communicate them effectively to all stakeholders involved in the manufacturing process.
- Iterative Optimization: Continuously monitor and evaluate machining performance, surface finish quality, and part dimensions to identify opportunities for optimizing stock allowances and refining machining processes iteratively.
- Use Simulation and Prototyping: Leverage simulation software and prototyping techniques to evaluate different stock allowance scenarios, validate machining strategies, and optimize stock allowance definitions based on empirical data and feedback.
- Stay Updated with Technology: Keep abreast of advancements in machining technology, cutting tools, CAM software, and materials science to leverage new opportunities for optimizing stock allowances and improving machining efficiency.
Conclusion
In conclusion, defining stock allowances is a critical aspect of machining operations, ensuring dimensional accuracy, surface finish quality, and process efficiency. By properly accounting for material variability, machining requirements, tool characteristics, and surface finish specifications, manufacturers can optimize stock allowances to achieve optimal machining performance and part quality. By adhering to best practices, addressing challenges, and leveraging simulation and prototyping techniques, manufacturers can refine stock allowance definitions iteratively, leading to improved productivity, cost savings, and competitiveness in today’s manufacturing landscape. Master the art of defining stock allowances, and unlock the full potential of your machining capabilities.