Mastering Toolpath Linking: A Comprehensive Guide to Seamless Machining Operations
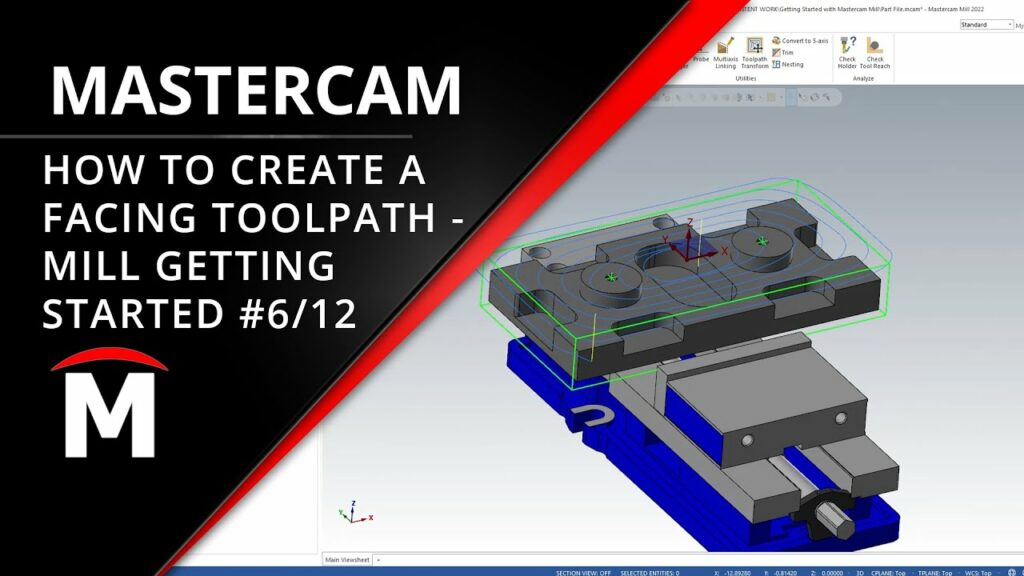
In the realm of computer-aided manufacturing (CAM), toolpath linking plays a crucial role in optimizing machining operations, ensuring smooth transitions between toolpath segments, minimizing tool wear, reducing machining time, and enhancing part quality. Toolpath linking refers to the strategies and techniques used to connect individual toolpath segments seamlessly, controlling tool motion, minimizing air cutting, and optimizing cutting conditions for maximum efficiency and precision. In this comprehensive guide, we’ll delve into the intricacies of toolpath linking, exploring its importance, methods, considerations, challenges, and best practices.
Understanding Toolpath Linking
Before delving into the details of toolpath linking, it’s essential to grasp its significance and objectives. Toolpath linking serves several key purposes:
- Minimizing Air Cutting: Toolpath linking minimizes unnecessary tool motion and air cutting between adjacent toolpath segments, reducing machining time, and improving efficiency.
- Optimizing Toolpath Transitions: By controlling tool motion and feed rate during transitions between toolpath segments, linking strategies ensure smooth, continuous machining operations and minimize surface imperfections.
- Improving Tool Life: Seamless toolpath linking reduces sudden changes in cutting forces and tool engagement, extending tool life and reducing tool wear and breakage.
- Enhancing Part Quality: Well-defined toolpath linking strategies result in improved surface finish quality, dimensional accuracy, and geometric precision, enhancing the overall quality of machined parts.
Importance and Benefits
Toolpath linking offers several key benefits that make it indispensable for modern machining operations:
- Efficiency: Efficient toolpath linking minimizes unnecessary tool travel and idle time between machining operations, reducing cycle times and increasing productivity.
- Precision: Seamless toolpath linking ensures consistent tool motion and cutting conditions, minimizing variations in surface finish and dimensional accuracy across the workpiece.
- Tool Protection: Controlled toolpath transitions and optimized cutting conditions protect cutting tools from excessive wear, chipping, and breakage, prolonging tool life and reducing tooling expenses.
- Process Stability: Well-defined toolpath linking strategies contribute to process stability, reducing the risk of vibrations, chatter, and surface defects during machining operations.
Methods for Creating Toolpath Linking
Creating effective toolpath linking involves several methods and considerations, depending on the specific requirements of the machining process and the characteristics of the workpiece:
- CAM Software Features: Most CAM software packages offer features and settings for defining toolpath linking parameters, including lead-in/out, corner smoothing, arc fitting, and transition controls.
- Toolpath Optimization Algorithms: Advanced CAM software utilizes optimization algorithms to automatically generate smooth, continuous toolpaths with minimal air cutting and optimized tool motion between machining operations.
- Manual Editing: In some cases, manual editing of toolpath segments may be necessary to fine-tune linking parameters, adjust toolpath trajectories, or optimize cutting conditions for specific machining requirements.
- Simulation and Verification: Performing simulation studies or virtual machining trials allows manufacturers to evaluate the effectiveness of toolpath linking strategies, verify toolpath trajectories, and identify potential issues or improvements before actual machining.
Challenges and Considerations
Creating seamless toolpath linking poses several challenges and considerations that must be addressed to ensure optimal machining results:
- Geometry Complexity: Machining complex geometries with sharp corners, tight radii, or intricate features requires careful consideration of toolpath linking strategies to ensure smooth transitions and avoid collisions.
- Material Properties: Variations in material properties such as hardness, ductility, and machinability may affect toolpath linking strategies, requiring adjustments to cutting parameters and linking parameters.
- Machine Tool Capabilities: Machine tool limitations, such as axis movement restrictions, acceleration/deceleration rates, and spindle speed capabilities, influence the feasibility and effectiveness of certain toolpath linking strategies.
- Toolpath Optimization: Balancing the need for efficient toolpath linking with machining requirements such as surface finish quality, dimensional accuracy, and tool life requires iterative optimization and fine-tuning of linking parameters.
- Operator Skill and Experience: Implementing effective toolpath linking strategies requires skill and experience in CAM programming, machining simulation, and toolpath optimization techniques.
Best Practices for Toolpath Linking
To maximize the effectiveness and reliability of toolpath linking, manufacturers should adhere to best practices:
- Start with Default Settings: Begin by using default toolpath linking settings provided by CAM software and gradually adjust parameters based on machining requirements and performance feedback.
- Iterative Optimization: Continuously monitor and evaluate machining performance, surface finish quality, and tool life to identify opportunities for optimizing toolpath linking parameters and refining machining processes iteratively.
- Simulation and Verification: Utilize simulation software and virtual machining tools to validate toolpath linking strategies, verify toolpath trajectories, and identify potential issues or improvements before actual machining.
- Collaborate Across Departments: Foster collaboration between design engineers, manufacturing engineers, CAM programmers, and machinists to ensure that toolpath linking strategies are accurately defined and integrated into machining processes.
- Stay Updated with Technology: Keep abreast of advancements in CAM software, machining technology, cutting tools, and materials science to leverage new opportunities for optimizing toolpath linking and improving machining efficiency.
Conclusion
In conclusion, toolpath linking is a critical aspect of CAM programming and machining optimization, ensuring efficient, precise, and reliable machining operations. By creating seamless transitions between toolpath segments, minimizing air cutting, and optimizing cutting conditions, manufacturers can achieve significant improvements in machining performance, part quality, and productivity. By adhering to best practices, addressing challenges, and leveraging simulation and verification techniques, manufacturers can refine toolpath linking strategies iteratively and unlock new levels of efficiency and competitiveness in today’s manufacturing landscape. Master the art of toolpath linking, and optimize your machining capabilities for success.