Unraveling the Art of Engraving Toolpaths: A Comprehensive Guide to Precision Machining
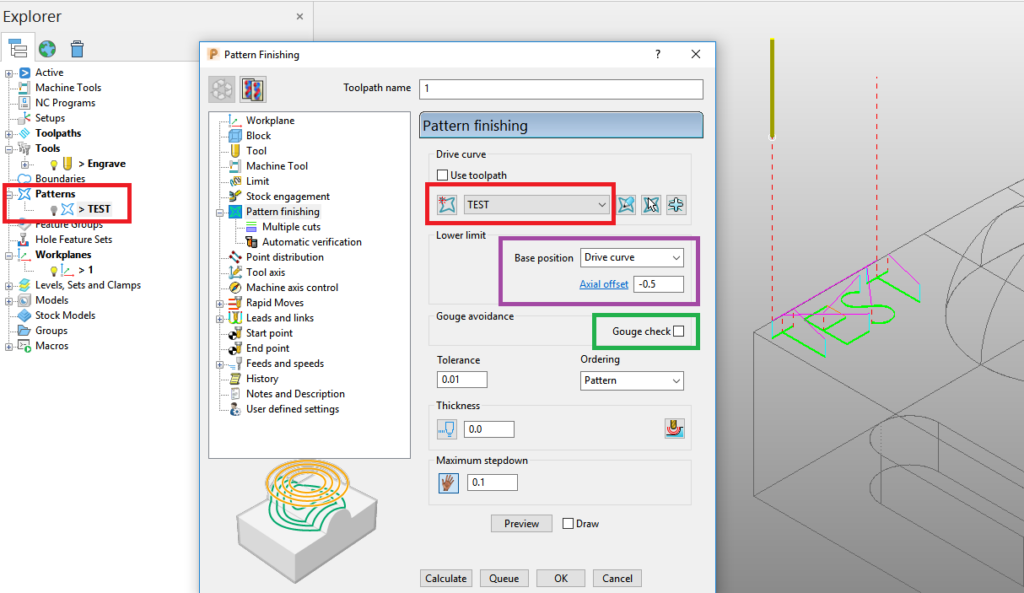
Engraving, an ancient art form dating back to the dawn of civilization, has evolved into a modern machining technique used across various industries, from jewelry making to aerospace manufacturing. Engraving toolpaths play a pivotal role in transforming digital designs into intricately carved surfaces, adding aesthetic value, functionality, and branding to a wide range of products and components. In this comprehensive guide, we’ll explore the nuances of creating engraving toolpaths, covering their significance, methods, considerations, challenges, and best practices.
Understanding Engraving Toolpaths
Engraving toolpaths are digital instructions that guide the movement of cutting tools, such as end mills, ball mills, or V-bits, to carve designs, text, or patterns onto workpiece surfaces. These toolpaths dictate the depth, width, and trajectory of each engraving stroke, translating design intent into tangible results with precision and accuracy. Engraving toolpaths can vary in complexity, from simple line engravings to intricate 3D reliefs, depending on the intricacy of the design and the capabilities of the machining equipment.
Importance and Benefits
Engraving toolpaths offer several key benefits that make them indispensable for modern machining operations:
- Customization: Engraving toolpaths enable the creation of customized designs, logos, serial numbers, or text, adding personalization and branding to products and components.
- Decoration: Engraving toolpaths are used to embellish surfaces with decorative patterns, textures, or motifs, enhancing aesthetics and visual appeal.
- Identification: Engraving toolpaths can be used to engrave part numbers, serial numbers, QR codes, or other identifiers for traceability and inventory management.
- Functional Features: Engraving toolpaths can create functional features such as keyways, grooves, or pockets for mating parts, assembly alignment, or component functionality.
- Surface Treatment: Engraving toolpaths can be employed for surface texturing, chamfering, or deburring, improving surface finish quality and tactile feel.
Methods for Creating Engraving Toolpaths
Creating engraving toolpaths involves several methods and considerations tailored to the specific requirements of the design and machining process:
- Design Preparation: Begin by preparing the design or artwork using graphic design software, CAD software, or 3D modeling software, ensuring that the design is suitable for engraving and meets the desired specifications.
- Toolpath Generation: Utilize CAM software to generate engraving toolpaths based on the design, selecting appropriate cutting tools, parameters, and strategies to achieve the desired engraving depth, width, and detail.
- Depth Control: Specify the engraving depth in the toolpath settings, taking into account material properties, cutting tool characteristics, and machining constraints to achieve the desired engraving effect.
- Toolpath Optimization: Optimize engraving toolpaths for efficiency, tool life, and surface finish quality, minimizing unnecessary tool travel, air cutting, and tool wear while maximizing material removal rates and machining accuracy.
- Simulation and Verification: Before machining, simulate and verify engraving toolpaths to ensure that the machining process is collision-free, compatible with machine tool capabilities, and aligned with design specifications.
Challenges and Considerations
Creating engraving toolpaths poses several challenges and considerations that must be addressed to ensure successful outcomes:
- Design Complexity: Intricate designs with fine details, small text, or complex geometries may require specialized engraving techniques and high-precision machining equipment to achieve accurate reproduction.
- Material Compatibility: Different materials, such as metals, plastics, wood, or ceramics, have unique machining properties and engraving requirements, necessitating adjustments to cutting parameters and toolpath strategies.
- Tool Selection: Selecting the appropriate cutting tools, including engraving bits, V-bits, or ball mills, is crucial for achieving the desired engraving depth, width, and detail while minimizing tool wear and breakage.
- Surface Finish Requirements: Engraving toolpaths must be optimized to meet surface finish requirements, minimizing machining marks, burrs, or surface defects that may detract from the visual appearance or functionality of the engraved surface.
- Toolpath Optimization: Balancing the need for efficient material removal with the desire for fine engraving detail requires careful optimization of cutting parameters, feed rates, spindle speeds, and toolpath strategies.
Best Practices for Engraving Toolpaths
To achieve optimal results in engraving machining, manufacturers should follow best practices:
- Design Optimization: Optimize designs for engraving by simplifying complex geometries, increasing line thickness, and minimizing fine details to improve engraving clarity and machining efficiency.
- Material Testing: Conduct material testing and experimentation to determine optimal cutting parameters, tooling, and machining strategies for specific materials and engraving applications.
- Depth Gradation: Gradually increase engraving depth in multiple passes to achieve uniform depth distribution, minimize tool deflection, and improve surface finish quality.
- Toolpath Simulation: Utilize simulation software and virtual machining tools to simulate and verify engraving toolpaths, identifying potential issues, optimizing parameters, and validating machining strategies before actual machining.
- Tool Maintenance: Regularly inspect and maintain cutting tools to ensure sharpness, accuracy, and performance consistency throughout the engraving process, replacing worn or damaged tools as needed.
Applications and Case Studies
Engraving toolpaths find applications across various industries and machining processes:
- Jewelry Making: Engraving toolpaths are used to create intricate designs, patterns, or text on precious metals such as gold, silver, and platinum for jewelry, watches, and accessories.
- Signage and Branding: Engraving toolpaths are employed to engrave logos, text, or graphics on signage, nameplates, plaques, and promotional items for branding, identification, or decoration.
- Tool and Die Making: Engraving toolpaths are utilized to engrave part numbers, serial numbers, or identifiers on tooling components, dies, molds, and stamping tools for traceability and inventory management.
- Aerospace and Defense: Engraving toolpaths are used to engrave part numbers, serial numbers, QR codes, or barcodes on aerospace components, defense equipment, and military hardware for identification and tracking purposes.
Conclusion
In conclusion, engraving toolpaths are a versatile and essential machining technique for adding aesthetic value, functionality, and branding to products and components across various industries. By mastering the art of engraving toolpath creation, manufacturers can unlock new possibilities for customization, decoration, and identification in their machining operations. Through careful design preparation, toolpath generation, simulation, and optimization, manufacturers can achieve precise, consistent, and visually striking engraving results that elevate the quality and appeal of their products. Embrace the art of engraving toolpaths, and unleash your creativity and craftsmanship in the world of precision machining.