Mastering Tolerance Analysis in 3DCS Variation Analyst: A Comprehensive Guide
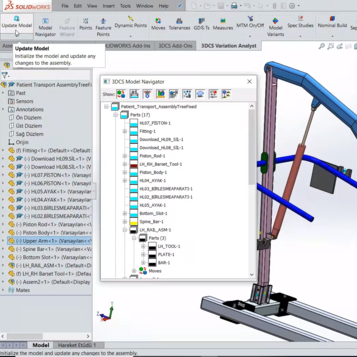
Introduction: Tolerance analysis plays a critical role in ensuring product quality, performance, and reliability in manufacturing industries. 3DCS Variation Analyst, a leading software solution for dimensional variation analysis, provides engineers and designers with powerful tools and capabilities to conduct comprehensive tolerance analysis and optimize product designs. In this extensive guide, we will delve into the fundamentals, methodologies, and advanced techniques for performing tolerance analysis in 3DCS Variation Analyst, covering everything from model setup to interpretation of results.
Section 1: Understanding Tolerance Analysis
1.1 Overview of Tolerance Analysis: Tolerance analysis is a systematic process of evaluating the impact of dimensional variations and tolerances on product performance and assembly quality. It involves predicting and quantifying the effects of manufacturing variations on product dimensions, fits, clearances, and functional requirements to ensure that design specifications are met within acceptable limits.
1.2 Importance of Tolerance Analysis: Tolerance analysis is essential for identifying and mitigating potential issues related to dimensional variation early in the design process, thereby reducing production costs, minimizing rework, and improving product quality and reliability. By performing tolerance analysis, engineers can optimize tolerances, improve assembly processes, and enhance product performance while meeting customer requirements and regulatory standards.
1.3 Role of 3DCS Variation Analyst: 3DCS Variation Analyst is a leading software tool specifically designed for dimensional variation analysis and tolerance optimization. It enables engineers to simulate and analyze the effects of dimensional variations, assembly processes, and manufacturing tolerances using advanced simulation techniques and statistical methods, providing valuable insights into product design and manufacturing processes.
Section 2: Tolerance Analysis Workflow in 3DCS Variation Analyst
2.1 Model Creation: The tolerance analysis process begins with creating a digital model of the product or assembly in 3DCS Variation Analyst. Engineers import CAD models or create simplified representations of parts, assemblies, and mating interfaces, including geometric features, surfaces, and tolerances.
2.2 Variation Modeling: Next, engineers define dimensional variations and tolerances for individual components and assembly features within the 3DCS Variation Analyst environment. They specify nominal dimensions, tolerance values, and distribution characteristics for each dimension, capturing the variability inherent in manufacturing processes.
2.3 Assembly Modeling: Engineers simulate the assembly process by defining assembly sequences, mating conditions, and contact relationships between components within the 3DCS Variation Analyst environment. They model part interactions, surface contacts, fastener constraints, and other assembly constraints to replicate real-world assembly conditions accurately.
2.4 Analysis Setup: Once the model is defined, engineers configure analysis settings, simulation parameters, and statistical methods within 3DCS Variation Analyst. They specify analysis objectives, such as dimensional compliance, fit and finish requirements, or functional performance criteria, and define output metrics for evaluating simulation results.
Section 3: Advanced Techniques and Methodologies
3.1 Monte Carlo Simulation: 3DCS Variation Analyst employs Monte Carlo simulation techniques to generate probabilistic variations in component dimensions and assembly configurations based on specified tolerances and distributions. Engineers perform multiple simulation runs to sample the parameter space and assess the variability of key performance metrics, such as part clearances, assembly stack-up, or dimensional compliance.
3.2 Sensitivity Analysis: Sensitivity analysis helps engineers identify the most influential factors contributing to dimensional variation and assembly quality. 3DCS Variation Analyst enables engineers to perform sensitivity analysis by varying individual tolerances or assembly parameters and observing their impact on product dimensions, fits, clearances, and functional requirements.
3.3 Worst-Case Analysis: In addition to probabilistic simulation, 3DCS Variation Analyst supports worst-case analysis methods for evaluating the extreme conditions and worst-case scenarios that may occur due to dimensional variations and tolerances. Engineers identify critical dimensions, tolerance stack-up paths, and potential failure modes to ensure that design specifications are met under worst-case conditions.
3.4 Statistical Analysis: 3DCS Variation Analyst provides statistical tools for analyzing simulation results and assessing the distribution of dimensional variations across the product or assembly. Engineers use statistical methods such as probability density functions (PDFs), cumulative distribution functions (CDFs), and tolerance histograms to quantify variability, estimate process capability, and evaluate design robustness.
Section 4: Interpretation of Results and Optimization Strategies
4.1 Results Visualization: 3DCS Variation Analyst offers powerful visualization tools for interpreting simulation results and communicating findings effectively. Engineers visualize variation propagation, tolerance stack-up, assembly clearances, and other key metrics using 3D graphics, color maps, histograms, and sensitivity plots, facilitating decision-making and design optimization.
4.2 Root Cause Analysis: Engineers conduct root cause analysis to identify the underlying sources of dimensional variation and assembly issues revealed by tolerance analysis results. They analyze geometric relationships, tolerance chains, mating conditions, and manufacturing processes to pinpoint critical factors contributing to dimensional variability and implement corrective actions.
4.3 Tolerance Optimization: Based on the insights gained from tolerance analysis, engineers refine product designs, optimize tolerances, and improve manufacturing processes to enhance product quality and performance. They iteratively adjust tolerances, redesign features, modify assembly sequences, or implement compensation strategies to minimize variation, reduce assembly costs, and maximize product reliability.
Section 5: Best Practices and Tips
5.1 Early Integration of Tolerance Analysis: Integrate tolerance analysis into the product development process early to identify and address dimensional variation issues at the design stage when changes are less costly and time-consuming to implement. Collaborate closely with design, engineering, and manufacturing teams to establish tolerance objectives, define critical features, and prioritize design modifications.
5.2 Model Simplification and Abstraction: Simplify and abstract complex assemblies and components to streamline tolerance analysis and improve simulation efficiency. Focus on critical features, mating interfaces, and high-risk areas where dimensional variations are most likely to occur, and use simplified representations or lumped-parameter models to capture key geometric relationships accurately.
5.3 Continuous Learning and Professional Development: Stay updated on the latest techniques, methodologies, and software updates in tolerance analysis and dimensional variation management. Invest in training, certification programs, and industry seminars to enhance your proficiency in 3DCS Variation Analyst, statistical analysis techniques, and tolerance optimization strategies.
Conclusion: Performing tolerance analysis in 3DCS Variation Analyst offers engineers and designers a powerful framework for evaluating dimensional variation, optimizing tolerances, and enhancing product quality and reliability. By mastering the fundamental principles, advanced techniques, and best practices discussed in this guide, engineers can leverage 3DCS Variation Analyst to conduct comprehensive tolerance analysis, improve design robustness, and drive innovation in manufacturing industries. With its intuitive interface, robust simulation capabilities, and powerful visualization tools, 3DCS Variation Analyst empowers engineers to tackle complex tolerance analysis challenges and deliver high-quality products that meet customer expectations and regulatory requirements.