Mastering Manufacturing: A Comprehensive Exploration of CAM (Computer-Aided Manufacturing) in SolidWorks
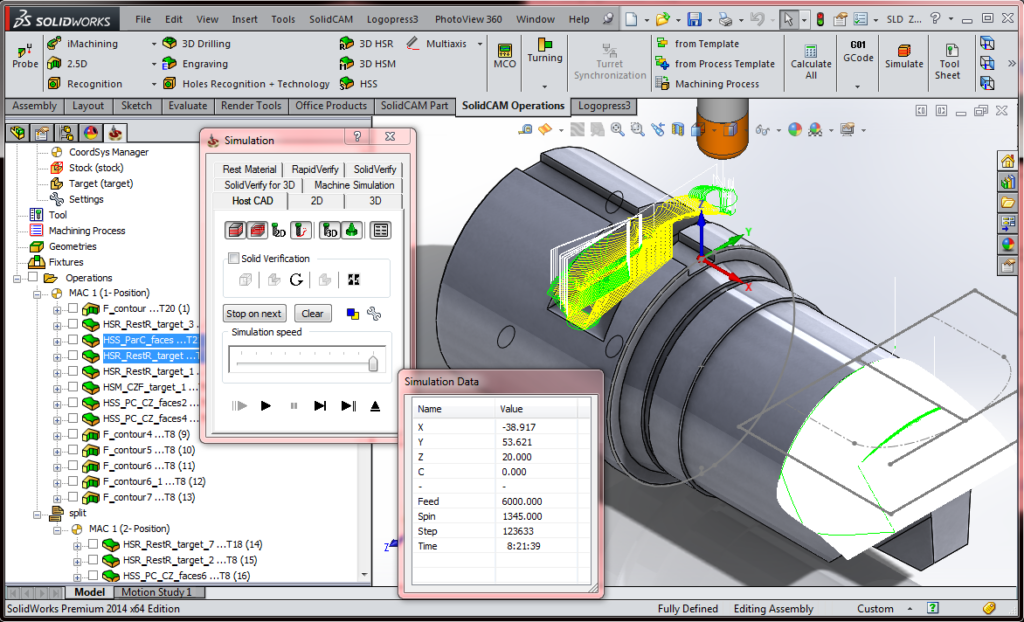
Computer-Aided Manufacturing (CAM) stands as a pivotal technology in modern manufacturing, revolutionizing the way designers and engineers translate digital designs into physical components with precision and efficiency. In this extensive exploration, we delve into the intricacies of CAM in SolidWorks, uncovering its functionalities, benefits, and practical applications across diverse industries and disciplines.
Understanding CAM in SolidWorks:
CAM in SolidWorks encompasses a suite of integrated tools and workflows designed to automate and optimize the manufacturing process, from CNC machining and 3D printing to sheet metal fabrication and additive manufacturing. By leveraging CAM functionalities, designers and engineers can generate toolpaths, simulate machining operations, and generate machine code directly from SolidWorks CAD models, streamlining the transition from design to production.
At its core, CAM in SolidWorks enables designers and engineers to harness the power of digital design data to drive manufacturing processes, ensuring accuracy, repeatability, and cost-effectiveness in the production of machined parts, prototypes, and production components. By integrating CAM seamlessly within the SolidWorks environment, designers can leverage familiar tools and workflows to optimize manufacturing operations, reduce lead times, and enhance overall productivity.
Key Concepts of CAM in SolidWorks:
- Toolpath Generation: CAM in SolidWorks includes tools for generating toolpaths, which define the motion of cutting tools such as end mills, drills, and routers during machining operations. Designers can specify machining parameters such as cutting speed, feed rate, and tool engagement to optimize toolpath generation for efficiency, surface finish, and tool life.
- Simulation and Verification: SolidWorks provides simulation and verification tools for visualizing and validating machining operations before execution. Designers can simulate toolpaths, check for collisions and tool interference, and verify machining operations against CAD models to ensure accuracy and avoid costly errors during production.
- Post-Processing and G-Code Generation: CAM in SolidWorks enables designers to post-process toolpaths and generate machine code, such as G-code, directly from SolidWorks CAD models. Designers can select machining strategies, specify machine configurations, and generate optimized toolpaths for CNC machining centers, 3D printers, and other manufacturing equipment.
- Multi-Axis Machining: SolidWorks supports multi-axis machining capabilities, allowing designers to create complex toolpaths for machining intricate geometries and freeform surfaces. Designers can leverage multi-axis machining strategies such as 3+2 and 5-axis simultaneous machining to achieve higher accuracy, surface finish, and productivity in manufacturing operations.
Benefits of CAM in SolidWorks:
- Streamlined Workflow: CAM in SolidWorks streamlines the workflow by integrating design and manufacturing within a single, cohesive environment. Designers can seamlessly transition from CAD modeling to CAM programming, eliminating the need for data translation, file conversions, and manual data transfer between software applications.
- Improved Accuracy and Precision: CAM in SolidWorks ensures accuracy and precision in manufacturing operations by leveraging digital design data to drive machining processes. Designers can simulate machining operations, verify toolpaths, and optimize cutting parameters to achieve tight tolerances, surface finish requirements, and dimensional accuracy in machined parts.
- Reduced Lead Times: SolidWorks facilitates faster time-to-market by accelerating the manufacturing process through CAM automation and optimization. Designers can generate toolpaths, simulate machining operations, and generate machine code directly from SolidWorks CAD models, reducing lead times and accelerating production schedules.
- Cost Reduction: CAM in SolidWorks helps reduce manufacturing costs by optimizing machining operations, minimizing material waste, and maximizing machine utilization. Designers can optimize cutting parameters, reduce setup times, and improve tool life to enhance productivity and efficiency in manufacturing processes, ultimately reducing production costs and improving profitability.
Practical Applications of CAM in SolidWorks:
- Precision Machining: SolidWorks supports precision machining applications across industries such as aerospace, automotive, and medical devices, enabling designers to manufacture complex components with tight tolerances and high precision. Designers leverage CAM to generate toolpaths, simulate machining operations, and produce precision parts for critical applications.
- Prototyping and Rapid Manufacturing: CAM in SolidWorks facilitates prototyping and rapid manufacturing by enabling designers to quickly translate digital designs into physical prototypes and production parts. Designers can leverage CAM automation and optimization to streamline the production of prototypes, short production runs, and customized components, reducing time-to-market and accelerating product development cycles.
- Tool and Die Making: SolidWorks supports tool and die making applications through CAM automation and optimization, enabling designers to manufacture molds, dies, and tooling components with precision and efficiency. Designers leverage CAM to generate toolpaths, simulate machining operations, and produce tooling components for injection molding, stamping, and forming processes.
- Custom Fabrication: CAM in SolidWorks facilitates custom fabrication applications such as woodworking, metalworking, and composite manufacturing, enabling designers to produce customized components and assemblies to meet unique design requirements. Designers leverage CAM automation and optimization to optimize cutting parameters, reduce material waste, and improve production efficiency in custom fabrication processes.
Conclusion:
CAM in SolidWorks represents a transformative technology within the realm of manufacturing, empowering designers and engineers to seamlessly translate digital designs into physical components with precision, efficiency, and reliability. By integrating CAM seamlessly within the SolidWorks environment, designers can leverage familiar tools and workflows to optimize manufacturing operations, reduce lead times, and enhance overall productivity. Whether used in precision machining, prototyping, tool and die making, or custom fabrication, CAM in SolidWorks enables designers to master the art of manufacturing, driving innovation, competitiveness, and excellence in engineering and manufacturing.