Mastering Hydraulic System Modeling and Simulation in AMESim: A Comprehensive Guide
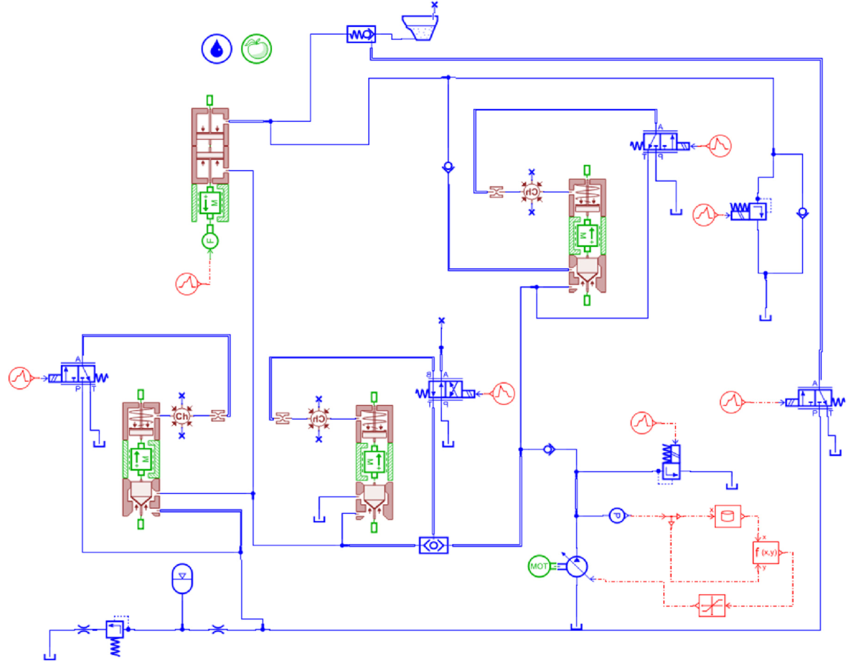
Introduction: Hydraulic systems play a crucial role in various engineering applications, including automotive, aerospace, industrial machinery, and renewable energy. Modeling and simulating hydraulic systems enable engineers to analyze performance, predict behavior, and optimize designs before physical prototyping and testing. AMESim, a leading multi-domain simulation software, provides powerful tools and capabilities for modeling and simulating hydraulic systems with accuracy and efficiency. In this comprehensive guide, we will explore the fundamentals, methodologies, and advanced techniques for modeling and simulating hydraulic systems in AMESim, covering everything from component modeling to system-level analysis.
Section 1: Understanding Hydraulic System Modeling
1.1 Overview of Hydraulic Systems: Hydraulic systems use pressurized fluid (usually oil) to transmit power and control mechanical motion in various applications, such as actuators, valves, pumps, and cylinders. Understanding the principles of fluid dynamics, thermodynamics, and control theory is essential for modeling hydraulic systems accurately.
1.2 Importance of Hydraulic System Modeling: Modeling hydraulic systems enables engineers to predict system behavior, evaluate performance under different operating conditions, and optimize design parameters for efficiency, reliability, and safety. By simulating hydraulic systems in AMESim, engineers can identify potential issues, troubleshoot problems, and improve system performance before implementation.
1.3 Role of AMESim in Hydraulic System Modeling: AMESim is a multi-domain simulation software that allows engineers to model complex dynamic systems, including hydraulic, pneumatic, mechanical, electrical, and control systems. Its intuitive graphical interface, extensive component libraries, and advanced simulation capabilities make it an ideal tool for modeling and simulating hydraulic systems in various engineering domains.
Section 2: Hydraulic Component Modeling in AMESim
2.1 Fluid Properties and Behavior: Modeling fluid properties and behavior is crucial for accurately simulating hydraulic systems. AMESim provides built-in fluid property models for common hydraulic fluids, allowing engineers to define viscosity, density, compressibility, and other fluid properties based on temperature, pressure, and fluid composition.
2.2 Hydraulic Components: AMESim offers a comprehensive library of hydraulic components, including pumps, valves, cylinders, motors, accumulators, filters, and pipes. Engineers can select and configure components from the library, specifying parameters such as flow rates, pressures, volumes, and control inputs to model specific hydraulic system configurations.
2.3 Component Behavior Modeling: Engineers define the dynamic behavior of hydraulic components using mathematical models based on physical principles and empirical data. AMESim provides modeling blocks and templates for representing component behavior, including flow resistances, pressure drops, volumetric efficiencies, and actuator dynamics, enabling engineers to simulate component response to input signals accurately.
Section 3: System-Level Hydraulic System Modeling
3.1 System Configuration and Integration: Engineers assemble hydraulic system models by integrating individual components into a system-level configuration within AMESim. They define interconnections, fluid paths, control loops, and boundary conditions to replicate real-world system behavior and interactions accurately.
3.2 Control Systems and Actuators: AMESim allows engineers to model control systems and actuators, including proportional, integral, and derivative (PID) controllers, servo valves, directional control valves, and hydraulic cylinders. Engineers specify control strategies, setpoints, feedback signals, and actuator commands to simulate closed-loop control of hydraulic systems and achieve desired performance objectives.
3.3 Hydraulic Circuit Design: Engineers design hydraulic circuits by arranging components, valves, and actuators in logical sequences to perform specific tasks, such as motion control, force generation, or energy conversion. AMESim’s schematic editor and graphical interface enable engineers to visualize and simulate hydraulic circuits, analyze fluid flow paths, and optimize system layouts for efficiency and reliability.
Section 4: Advanced Techniques and Analysis in AMESim
4.1 Transient and Steady-State Analysis: AMESim supports transient and steady-state analysis of hydraulic systems, allowing engineers to simulate system response over time and evaluate dynamic behavior under transient conditions, such as startup, shutdown, or load changes. Engineers analyze key performance metrics, including pressures, flows, velocities, temperatures, and energy consumption, to assess system stability, performance, and efficiency.
4.2 Fault Diagnosis and Troubleshooting: AMESim enables engineers to diagnose faults and troubleshoot issues in hydraulic systems by simulating abnormal operating conditions, component failures, or system malfunctions. Engineers introduce faults such as leaks, valve stiction, pump cavitation, or sensor errors into the model and analyze system response to identify root causes and implement corrective actions.
4.3 Optimization and Design Exploration: Engineers use AMESim’s optimization tools and design exploration capabilities to improve hydraulic system performance, efficiency, and reliability. They perform parametric studies, sensitivity analyses, and design optimizations to identify optimal design parameters, validate design requirements, and maximize system performance while minimizing cost and energy consumption.
Section 5: Best Practices and Tips
5.1 Model Validation and Verification: Validate and verify hydraulic system models by comparing simulation results with experimental data, analytical solutions, or manufacturer specifications. Conduct sensitivity analyses, uncertainty quantification, and model validation tests to ensure that simulation results are accurate, reliable, and representative of real-world behavior.
5.2 Modular and Hierarchical Modeling: Organize hydraulic system models into modular and hierarchical structures to improve model scalability, maintainability, and reusability. Divide complex systems into smaller subsystems, components, and interfaces, and use AMESim’s hierarchical modeling features to encapsulate functionality, simplify model architecture, and facilitate collaboration among team members.
5.3 Continuous Learning and Professional Development: Stay updated on the latest developments, best practices, and advanced techniques in hydraulic system modeling and simulation. Participate in training programs, webinars, conferences, and user forums to enhance your proficiency in AMESim, fluid dynamics, control theory, and hydraulic system design.
Conclusion: Modeling and simulating hydraulic systems in AMESim offer engineers and designers a powerful framework for analyzing performance, predicting behavior, and optimizing designs in various engineering applications. By mastering the fundamental principles, advanced techniques, and best practices discussed in this guide, engineers can leverage AMESim to simulate complex hydraulic systems accurately, troubleshoot problems effectively, and improve system performance, efficiency, and reliability. With its intuitive interface, extensive component libraries, and advanced simulation capabilities, AMESim empowers engineers to tackle challenging hydraulic system design and optimization tasks and drive innovation in engineering industries.