Mastering the Art of Mold and Die Machining: A Comprehensive Guide
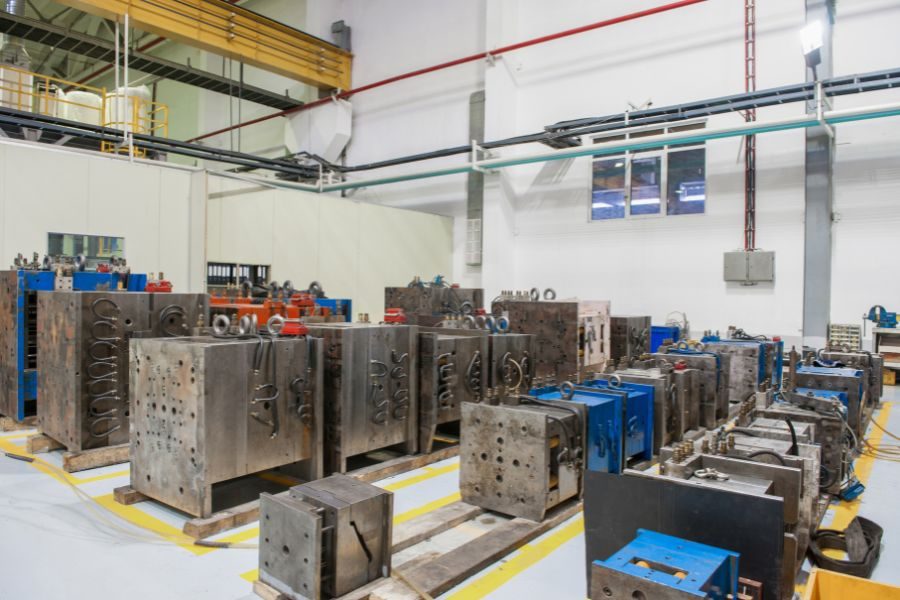
Molds and dies play a critical role in modern manufacturing, serving as the foundation for producing a wide range of components, products, and parts across various industries. From automotive components to consumer electronics, molds and dies enable the mass production of complex geometries with precision and consistency. Machining molds and dies requires specialized knowledge, techniques, and equipment to achieve the required accuracy, surface finish, and dimensional integrity. In this comprehensive guide, we’ll delve into the intricacies of mold and die machining, covering its importance, methods, challenges, best practices, and applications.
Understanding Mold and Die Machining
Mold and die machining involves the fabrication of molds, dies, and tooling components used in the manufacturing process. Molds are used to shape materials such as plastics, metals, and composites into specific forms, while dies are used to cut, form, or stamp materials into desired shapes or profiles. Machining molds and dies typically involves processes such as milling, turning, drilling, grinding, and EDM (Electrical Discharge Machining) to achieve the required geometries, tolerances, and surface finishes.
Importance of Mold and Die Machining
Mold and die machining is crucial for several reasons:
- Productivity: Well-designed and machined molds and dies enable efficient and repeatable production processes, leading to higher productivity and throughput.
- Precision: Molds and dies must be machined to tight tolerances and precise geometries to ensure the dimensional accuracy and quality of the final products.
- Versatility: Molds and dies can be used to produce a wide range of components and parts across different industries, providing versatility and flexibility in manufacturing operations.
- Innovation: Advances in mold and die machining techniques, materials, and technologies drive innovation in product design, manufacturing processes, and material utilization.
- Cost-effectiveness: Machining molds and dies allows for the production of high-quality, custom tooling solutions at a competitive cost, compared to other manufacturing methods.
Methods for Machining Molds and Dies
Machining molds and dies involves several methods and techniques tailored to the specific requirements of the workpiece and machining process:
- CAD/CAM Design: Begin with the design of the mold or die using CAD (Computer-Aided Design) software, incorporating features, dimensions, and specifications based on the requirements of the final product.
- Material Selection: Choose the appropriate material for the mold or die based on factors such as material properties, durability, machinability, and surface finish requirements.
- Toolpath Generation: Utilize CAM software to generate toolpaths for machining operations, selecting cutting strategies, tooling, and parameters to achieve the desired geometries and surface finishes.
- Machining Operations: Perform machining operations such as milling, turning, drilling, grinding, and EDM to remove material, shape features, and achieve the final dimensions and surface finishes of the mold or die.
- Finishing Processes: After rough machining, apply finishing processes such as polishing, lapping, or coating to improve surface finish quality, remove machining marks, and enhance durability and wear resistance.
Challenges and Considerations
Machining molds and dies presents several challenges and considerations that must be addressed to ensure successful outcomes:
- Complex Geometries: Molds and dies often feature complex geometries, intricate details, and tight tolerances, requiring advanced machining techniques and high-precision equipment.
- Material Hardness: Some mold and die materials, such as hardened tool steels, can be challenging to machine due to their high hardness and abrasiveness, necessitating specialized tooling and machining strategies.
- Heat Generation: Machining processes such as milling and grinding generate heat, which can affect the dimensional stability, surface integrity, and material properties of the mold or die, requiring proper cooling and lubrication techniques.
- Tool Wear and Breakage: High-speed machining of hard materials can lead to accelerated tool wear, chipping, and breakage, impacting machining efficiency and tool life.
- Surface Finish Requirements: Molds and dies often require fine surface finishes to produce high-quality parts, requiring careful selection of cutting tools, feeds, speeds, and finishing processes.
Best Practices for Mold and Die Machining
To achieve optimal results in mold and die machining, manufacturers should follow best practices:
- Collaborative Design: Foster collaboration between design engineers, CAM programmers, and machinists to ensure that mold and die designs are optimized for manufacturability and machining efficiency.
- Material Handling: Handle and secure mold and die materials with care to minimize distortion, damage, or contamination during machining operations.
- Toolpath Optimization: Optimize toolpaths and cutting parameters to minimize cycle times, reduce tool wear, and achieve the required surface finishes and tolerances.
- Coolant and Lubrication: Use appropriate coolant and lubrication techniques to dissipate heat, reduce friction, and prolong tool life during machining operations.
- Quality Control: Implement rigorous quality control measures, including dimensional inspection, surface roughness measurement, and material analysis, to ensure that machined molds and dies meet design specifications and quality standards.
Applications and Case Studies
Mold and die machining finds applications across various industries and manufacturing processes:
- Injection Molding: Molds for injection molding processes are machined to precise tolerances to produce plastic components for automotive, consumer electronics, medical devices, and packaging applications.
- Die Casting: Dies for die casting processes are machined to shape metal alloys into complex parts for aerospace, automotive, industrial, and consumer goods industries.
- Stamping and Forming: Dies for stamping and forming operations are used to shape sheet metal components for automotive body panels, appliances, electronics, and construction materials.
- Blow Molding: Molds for blow molding processes are machined to create hollow plastic parts for bottles, containers, and packaging solutions across various industries.
Conclusion
In conclusion, mold and die machining is a critical aspect of modern manufacturing, enabling the production of high-quality, precision components and products across diverse industries. By leveraging advanced CAD/CAM technologies, machining techniques, and best practices, manufacturers can optimize mold and die fabrication processes, enhance productivity, and maintain a competitive edge in today’s global marketplace. Mastering the art of mold and die machining requires expertise, innovation, and a commitment to excellence in every aspect of the manufacturing process.