How to Simulate Fluid Flow Using ANSYS Fluent
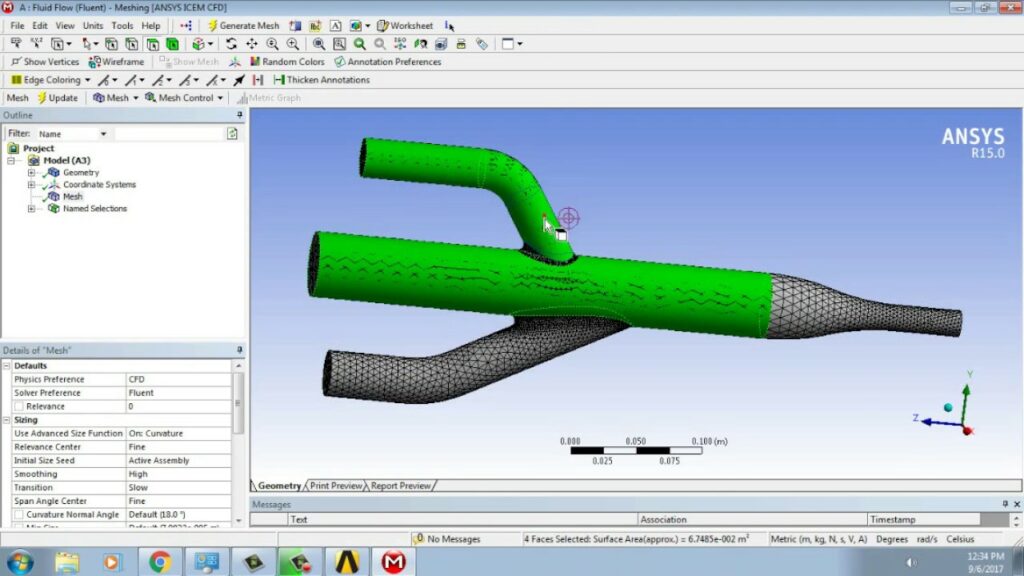
Simulating fluid flow using ANSYS Fluent is a crucial capability for engineers and researchers across various industries, including aerospace, automotive, energy, and manufacturing. ANSYS Fluent is a powerful computational fluid dynamics (CFD) software that enables users to analyze and predict the behavior of fluid flows, heat transfer, and related phenomena. This comprehensive guide will walk you through the step-by-step process of setting up and conducting fluid flow simulations using ANSYS Fluent, covering pre-processing, solution setup, post-processing, and interpretation of results.
Table of Contents
- Introduction to Fluid Flow Simulation
- Preparing Geometry for Simulation
- Setting Up Fluid Flow Simulation in ANSYS Fluent
- Defining Boundary Conditions
- Solving the Fluid Flow Simulation
- Post-Processing and Analyzing Results
- Advanced Simulation Techniques
- Troubleshooting and Common Issues
- Conclusion
1. Introduction to Fluid Flow Simulation
Fluid flow simulation involves using numerical methods to solve the governing equations of fluid dynamics, such as the Navier-Stokes equations, to predict fluid behavior under various conditions. ANSYS Fluent provides a comprehensive suite of tools and solvers for simulating laminar and turbulent flows, multiphase flows, heat transfer, combustion, and more. Applications range from aerodynamics of vehicles and aircraft to thermal management in electronic devices and environmental fluid dynamics.
2. Preparing Geometry for Simulation
- Import CAD Geometry:
- Import the geometry of the fluid domain into ANSYS Fluent.
- Supported formats include STEP, IGES, Parasolid, and native CAD formats.
- Geometry Cleanup:
- Ensure the geometry is clean and watertight, with no gaps or overlapping surfaces.
- Use ANSYS DesignModeler or SpaceClaim for geometry cleanup if necessary.
- Simplify Geometry:
- Simplify complex geometries or assemblies to improve mesh quality and computational efficiency.
3. Setting Up Fluid Flow Simulation in ANSYS Fluent
- Launch ANSYS Fluent:
- Start ANSYS Fluent from the ANSYS Workbench or as a standalone application.
- Create New Case:
- Set up a new case or open an existing project for fluid flow simulation.
- Select Physics Models:
- Choose the appropriate fluid model (e.g., laminar, turbulent) and specify material properties (density, viscosity) for the fluid.
- Define Solver Settings:
- Configure numerical settings such as discretization schemes (e.g., finite volume method), solution methods (e.g., pressure-velocity coupling), and convergence criteria.
4. Defining Boundary Conditions
- Inlet Conditions:
- Specify inlet boundary conditions including flow rate, velocity profile, temperature, and species concentrations if applicable.
- Outlet Conditions:
- Define outlet conditions such as pressure, backflow conditions, and temperature if applicable.
- Wall Conditions:
- Set boundary conditions for walls including no-slip (velocity equals zero), adiabatic or isothermal walls, roughness specifications, and heat flux if needed.
- Additional Boundaries:
- Define other boundaries such as symmetry planes, periodic boundaries, or interfaces for multiphase flows.
5. Solving the Fluid Flow Simulation
- Initialize Solution:
- Initialize the flow field using appropriate initialization methods (e.g., uniform initial conditions, restart from previous solution).
- Iterative Solution Process:
- Start the solver to iterate and solve the governing equations for fluid flow.
- Monitor solution convergence and adjust solver settings if necessary to achieve convergence.
6. Post-Processing and Analyzing Results
- Visualize Results:
- Use ANSYS Fluent post-processing tools to visualize flow field properties such as velocity vectors, pressure contours, temperature distributions, and species concentrations.
- Generate Reports:
- Generate comprehensive reports and plots to summarize simulation results and key performance metrics.
- Extract Quantitative Data:
- Extract quantitative data such as drag coefficients, lift forces, heat transfer coefficients, and mass flow rates from the simulation results.
7. Advanced Simulation Techniques
- Turbulence Modeling:
- Select appropriate turbulence models (e.g., k-epsilon, k-omega) to accurately capture turbulent flow characteristics.
- Perform mesh sensitivity studies and validate turbulence models against experimental data if required.
- Multiphase Flows:
- Simulate multiphase flows involving two or more immiscible fluids or phases (e.g., air-water, oil-gas).
- Define phase interactions, surface tension effects, and phase change phenomena (evaporation, condensation).
- Heat Transfer Analysis:
- Incorporate heat transfer mechanisms such as conduction, convection, and radiation into fluid flow simulations.
- Model heat sources, heat sinks, and thermal boundary conditions for accurate thermal analysis.
8. Troubleshooting and Common Issues
- Convergence Issues:
- Address convergence problems by adjusting mesh resolution, relaxation factors, and solver tolerances.
- Check mesh quality and boundary conditions for potential issues affecting solution convergence.
- Boundary Condition Errors:
- Validate boundary conditions to ensure they accurately represent physical conditions and match experimental data if available.
- Mesh Quality Concerns:
- Review mesh quality metrics (e.g., skewness, aspect ratio) and refine the mesh if poor quality elements are detected.
- Use ANSYS Fluent tools for mesh diagnostics and quality improvement.
9. Conclusion
Simulating fluid flow using ANSYS Fluent offers engineers and researchers a powerful toolset for analyzing and predicting complex fluid dynamics phenomena across diverse applications. By following the steps outlined in this guide, you can effectively set up, solve, and analyze fluid flow simulations using ANSYS Fluent, from geometry preparation to result interpretation. Understanding the nuances of physics modeling, boundary condition definition, solver setup, and post-processing techniques enables users to obtain accurate insights into flow behavior, optimize designs, and make informed engineering decisions. ANSYS Fluent’s robust capabilities and advanced features make it a preferred choice for CFD simulations, supporting innovation and reliability in product development, research, and engineering analysis.