How to Perform Thermal Analysis in ANSYS
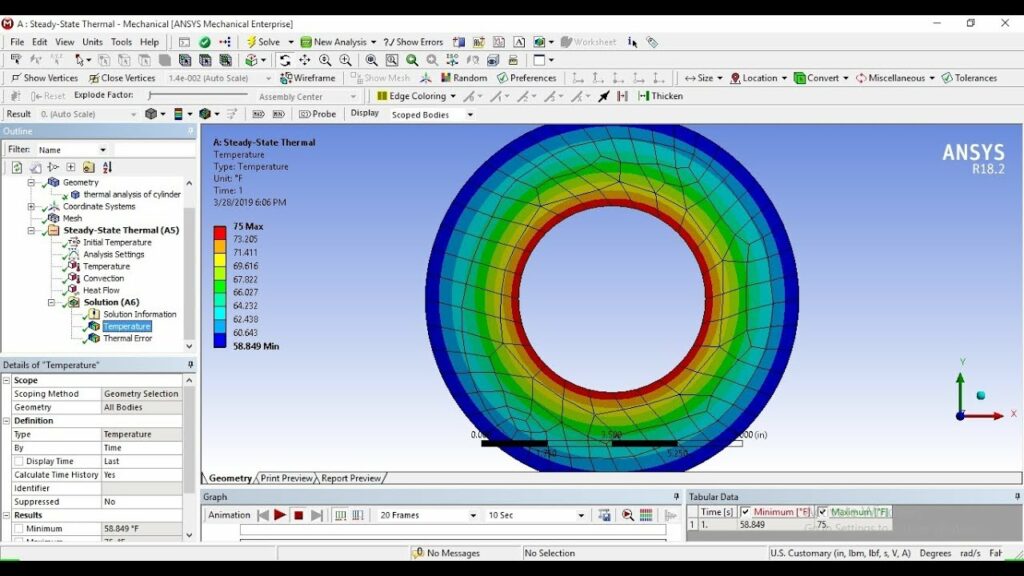
Performing thermal analysis in ANSYS is essential for engineers and designers across various industries to evaluate and optimize the thermal performance of components, systems, and processes. ANSYS provides powerful tools and capabilities for simulating heat transfer, thermal management, and thermal effects on structural integrity. This comprehensive guide will walk you through the step-by-step process of setting up and conducting thermal analysis using ANSYS, covering theory, pre-processing, solution setup, post-processing, and interpretation of results.
Table of Contents
- Introduction to Thermal Analysis
- Preparing Geometry for Thermal Analysis
- Setting Up Thermal Analysis in ANSYS
- Defining Boundary Conditions
- Solving the Thermal Analysis
- Post-Processing and Analyzing Results
- Advanced Thermal Analysis Techniques
- Troubleshooting and Common Issues
- Conclusion
1. Introduction to Thermal Analysis
Thermal analysis in ANSYS involves simulating heat transfer mechanisms such as conduction, convection, and radiation to predict temperature distributions, thermal stresses, and thermal deformations in structures or components. Understanding thermal behavior is crucial for ensuring thermal management, optimizing cooling strategies, and preventing overheating in engineering applications across industries such as aerospace, automotive, electronics, and manufacturing.
2. Preparing Geometry for Thermal Analysis
- Import CAD Geometry:
- Import the CAD geometry of the component or system into ANSYS.
- Supported formats include STEP, IGES, Parasolid, and native CAD formats.
- Geometry Cleanup:
- Ensure the geometry is clean and free from any gaps or overlaps that may affect mesh quality and analysis results.
- Use ANSYS DesignModeler or SpaceClaim for geometry cleanup if necessary.
- Simplify Geometry:
- Simplify complex features or assemblies to reduce computational resources and enhance mesh quality.
3. Setting Up Thermal Analysis in ANSYS
- Launch ANSYS Workbench:
- Start ANSYS Workbench and create a new project for thermal analysis.
- Physics Settings:
- Select the thermal analysis module (ANSYS Mechanical or ANSYS Fluent) depending on the application requirements.
- Define material properties such as thermal conductivity, specific heat capacity, and thermal expansion coefficient.
- Solver Settings:
- Configure solver settings including solution controls, convergence criteria, and solution methods (e.g., steady-state or transient analysis).
4. Defining Boundary Conditions
- Initial Conditions:
- Specify initial temperatures for the components or system before applying thermal loads.
- Ensure initial conditions reflect the starting thermal state based on operational scenarios.
- Boundary Conditions:
- Define thermal boundary conditions such as:
- Heat fluxes or heat sources applied to surfaces or volumes.
- Temperature distributions on boundaries (Dirichlet boundary conditions).
- Convective heat transfer coefficients and ambient temperatures for convection boundary conditions.
- Define thermal boundary conditions such as:
- Radiation Settings:
- Include radiation effects if applicable, specifying emissivity values and surface properties for radiative heat transfer analysis.
5. Solving the Thermal Analysis
- Mesh Generation:
- Generate a finite element mesh on the geometry using ANSYS Meshing or TGrid.
- Ensure mesh quality meets ANSYS recommended criteria (e.g., aspect ratio, skewness) for accurate thermal analysis results.
- Solver Execution:
- Launch the solver to perform the thermal analysis simulation.
- Monitor solver progress and convergence status to ensure the analysis completes successfully.
6. Post-Processing and Analyzing Results
- Temperature Distribution:
- Visualize temperature distributions across the component or system using ANSYS post-processing tools.
- Identify hot spots, thermal gradients, and critical temperature levels affecting performance or reliability.
- Heat Flux and Heat Transfer Analysis:
- Analyze heat flux patterns and conduct heat transfer calculations to evaluate thermal loads and energy dissipation.
- Thermal Stress and Deformation:
- Evaluate thermal stresses and thermal deformations induced by temperature gradients using structural analysis capabilities in ANSYS Mechanical.
7. Advanced Thermal Analysis Techniques
- Transient Thermal Analysis:
- Perform transient thermal analysis to simulate temperature changes over time due to varying thermal loads or operational conditions.
- Study thermal response during startup, shutdown, or transient heat transfer scenarios.
- Conjugate Heat Transfer:
- Model conjugate heat transfer phenomena involving fluid flow and thermal conduction in solid structures.
- Coupled simulations between ANSYS Fluent (for fluid flow) and ANSYS Mechanical (for structural analysis) facilitate accurate thermal-fluid interaction studies.
- Thermal-Electric Coupling:
- Incorporate thermal-electric coupling effects in simulations involving electronic components or devices to analyze temperature rise due to electrical power dissipation.
8. Troubleshooting and Common Issues
- Convergence Issues:
- Address convergence problems by refining the mesh, adjusting solver settings, or optimizing boundary conditions.
- Ensure numerical stability and solution accuracy throughout the thermal analysis process.
- Mesh Quality Problems:
- Resolve mesh quality issues by refining the mesh in critical regions or using adaptive meshing techniques.
- Check element aspect ratios, skewness, and element distortions affecting thermal analysis results.
- Material Properties:
- Validate material properties such as thermal conductivity and specific heat capacity to accurately represent material behavior under thermal loading.
9. Conclusion
Thermal analysis using ANSYS offers engineers a powerful toolset for predicting and optimizing thermal performance in diverse engineering applications. By following the steps outlined in this guide, you can effectively perform thermal simulations using ANSYS, from geometry preparation to result interpretation. Understanding the fundamentals of thermal behavior, boundary condition definition, solver setup, and advanced simulation techniques empowers engineers to simulate realistic thermal scenarios, optimize designs, and make informed decisions to enhance product reliability and performance. ANSYS’s robust capabilities in thermal analysis support innovation and engineering excellence across industries, enabling engineers to tackle complex thermal challenges with confidence and precision.