How to Conduct Modal Analysis in ANSYS
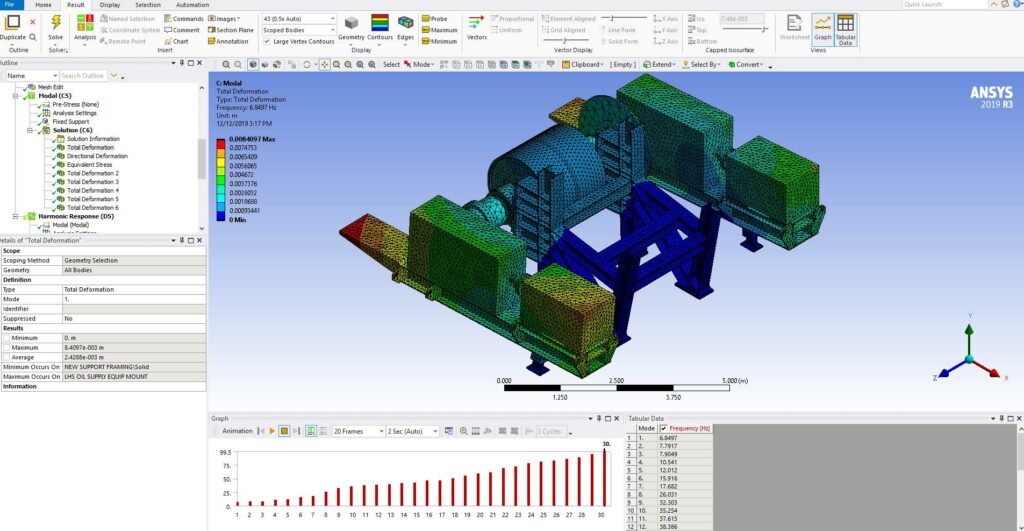
Modal analysis is a crucial engineering tool used to study the dynamic characteristics of structures and components. It helps engineers understand natural frequencies, mode shapes, and damping effects, which are essential for ensuring structural integrity, avoiding resonance, and optimizing designs. ANSYS, a leading simulation software, provides powerful capabilities for performing modal analysis across various industries such as aerospace, automotive, mechanical engineering, and civil engineering. This comprehensive guide will walk you through the step-by-step process of conducting modal analysis using ANSYS, covering theory, pre-processing, solution setup, post-processing, and interpretation of results.
Table of Contents
- Introduction to Modal Analysis
- Preparing Geometry for Analysis
- Setting Up Modal Analysis in ANSYS
- Solving the Modal Analysis
- Post-Processing and Analyzing Results
- Advanced Modal Analysis Techniques
- Troubleshooting and Common Issues
- Conclusion
1. Introduction to Modal Analysis
Modal analysis is a technique used to determine the natural frequencies and mode shapes of a structure or component. It involves studying how the structure vibrates in its natural modes of oscillation when subjected to dynamic forces or impulses. The results of modal analysis are crucial for:
- Identifying critical frequencies that may lead to resonance and structural failure.
- Optimizing structural designs to avoid unwanted vibrations and improve performance.
- Understanding the dynamic behavior of structures under operational conditions.
2. Preparing Geometry for Analysis
- Import CAD Geometry:
- Import the CAD geometry of the structure into ANSYS.
- Supported formats include STEP, IGES, Parasolid, and native CAD formats.
- Geometry Cleanup:
- Ensure the geometry is clean and free from any gaps or overlaps that may affect mesh quality and analysis results.
- Use ANSYS DesignModeler or SpaceClaim for geometry cleanup if necessary.
- Simplify Geometry:
- Simplify complex features or assemblies to reduce computational resources and enhance mesh quality.
3. Setting Up Modal Analysis in ANSYS
- Modal Analysis Setup:
- Launch ANSYS Workbench or Mechanical APDL.
- Create a new static structural analysis system or open an existing one.
- Define Material Properties:
- Assign material properties to the components of the model.
- Specify material types (e.g., isotropic, orthotropic) and input material constants such as Young’s modulus and Poisson’s ratio.
- Mesh Generation:
- Generate a finite element mesh on the geometry using ANSYS Meshing or TGrid.
- Choose appropriate element types (e.g., tetrahedral, hexahedral) and refine the mesh in critical regions for accurate modal analysis results.
4. Solving the Modal Analysis
- Setup Modal Analysis:
- Define the modal analysis settings including:
- Number of modes to extract.
- Desired frequency range.
- Solver options and convergence criteria.
- Define the modal analysis settings including:
- Run the Analysis:
- Launch the solver to perform the modal analysis.
- Monitor the solution progress and convergence status to ensure the analysis completes successfully.
5. Post-Processing and Analyzing Results
- Review Mode Shapes:
- Visualize and interpret mode shapes to understand how the structure vibrates at different natural frequencies.
- Identify the predominant displacements and deformation patterns associated with each mode.
- Natural Frequencies:
- Evaluate natural frequencies extracted from the modal analysis results.
- Identify critical frequencies that may coincide with operational frequencies or lead to resonance.
- Mode Participation Factors:
- Analyze mode participation factors to determine the contribution of each mode to the overall response of the structure.
6. Advanced Modal Analysis Techniques
- Complex Modes:
- Perform complex modal analysis to account for damping effects and complex eigenvalue problems.
- Frequency Response Analysis:
- Extend modal analysis to frequency response analysis to study the structure’s response to harmonic excitations.
- Random Vibration Analysis:
- Use modal analysis results as input for random vibration analysis to assess structural responses to stochastic loading conditions.
7. Troubleshooting and Common Issues
- Convergence Issues:
- Address convergence problems by adjusting solver settings, refining the mesh, or reviewing boundary conditions.
- Mode Shape Distortions:
- Review mesh quality and element types to minimize mode shape distortions caused by numerical artifacts.
- Unexpected Results:
- Validate material properties, boundary conditions, and load definitions to ensure they accurately represent the operational conditions.
8. Conclusion
Modal analysis in ANSYS provides engineers with valuable insights into the dynamic behavior of structures and components. By following the steps outlined in this guide, you can effectively set up and conduct modal analysis simulations using ANSYS, from geometry preparation to result interpretation. Understanding natural frequencies, mode shapes, and mode participation factors helps optimize designs, ensure structural integrity, and mitigate risks associated with vibrations and resonance. ANSYS’s robust capabilities for modal analysis make it a preferred choice for engineering simulations across diverse industries, supporting innovation and reliability in product development and design optimization.